Applications
Optimizing Monoclonal Antibody Production with Applikon Bioreactors
The production of monoclonal antibodies (mAbs) involves a series of carefully coordinated steps, from selecting a specific antigen target to cultivating antibody-producing cells and purifying the final product. Let’s explore how Applikon’s single-use and multi-use bioreactors can optimize each stage of the mAbs manufacturing process, making it more efficient and beneficial for customers.
Selecting and Preparing the Bioreactor System and Antigen
The first and crucial step in how to make monoclonal antibodies involves choosing the most suitable equipment based on the product and the goals of the bioprocess. Options include batch, fed-batch, perfusion, or chemostat processes. Applikon bioreactors support all these process forms, ensuring maximum productivity and flexibility to meet various production needs. Identifying and preparing the specific antigen that the monoclonal antibody will target involves finding a unique marker associated with the disease. Optimizing antigen selection and preparation with Applikon allows for quick and accurate identification of markers, enhancing the accuracy and efficiency of the produced antibodies.
Generating and Selecting High-Performance Cells
Producing monoclonal antibodies primarily uses Chinese hamster ovary (CHO) cells as production organism. Advanced biotechnological techniques such as transcriptomics, proteomics, and methotrexate-based amplification are used to enhance the expression of genetic factors and significantly increase the productivity of monoclonal Antibodies. CHO cells are extensively used in the biopharmaceutical industry due to their exceptional ability to perform complex post-translational modifications, which are crucial for the functional efficacy of therapeutic proteins. Although there are other production organisms, CHO cells are the preferred option for mAB production. The hybridoma technology, for example, which involves fusing B-cells that produce a specific antibody with myeloma cells, creates hybrid cells capable of continuous production. Although foundational in enabling the production of specific antibodies, the hybridoma method is less scalable compared to the production with CHO cells. The scalability and adaptability of CHO cells in large-scale manufacturing provides a more efficient and versatile platform for antibody production. This approach illustrates the steps to produce monoclonal antibodies effectively in modern biotechnological contexts, emphasizing scalability and precision.
Optimized Cell Expansion and Cultivation
Once the optimal cells are selected, expanding and cultivating them under ideal conditions is critical for high-quality mAb production with high yields. Applikon bioreactors provide precise control over temperature, pH, and dissolved oxygen levels, which are essential for maximizing cell growth and antibody yield. This optimized environment supports robust cell expansion and efficient antibody production, ensuring a consistent and reliable supply of mAbs.
Why Choose the Applikon AppliFlex ST Single-Use Bioreactor for mAb Manufacturing?
The Applikon AppliFles ST single-use bioreactor stands out in the monoclonal antibodies manufacturing landscape for several reasons:
- Precision and control: It offers unique control over environmental conditions, ensuring optimal cell growth and productivity.
- Scalability: Available in different volumes, it offers the scientist the opportunity to develop a process and subsequently scale it up to commercial-scale mAb production.
- Efficiency: The AppliFlex ST allows you to dive straight into your bioprocess thanks to a quick setup and easy operation. This reduces production times and costs, enhancing the overall efficiency of the mAb manufacturing process.
- Versatility: Thanks to customization options the AppliFlex ST bioreactor is a versatile tool for different mAb production processes, supporting a wide range of cell types and cultivation strategies.
Benefits of Using the Applikon Bioreactor
In conclusion, the monoclonal antibody production process represents a highlight of biotechnological innovation, with the Applikon AppliFles ST single-use bioreactor playing a critical role in enabling the efficient and scalable production and development of these vital therapeutic agents. As a leading monoclonal antibodies manufacturer, embracing the capabilities of the Applikon bioreactors can significantly enhance the efficiency, yield, and quality of mAb production, positioning manufacturers at the forefront of biopharmaceutical development. Discover how the Applikon AppliFlex ST single-use bioreactor can transform your mAb manufacturing process.
Feautured Products
SUPR single-use bioreactor
The SUPR single-use production bioreactor impresses with its simple, scalable and customer-friendly design. The cell culture reactor enables a seamless process transfer from R&D to production.
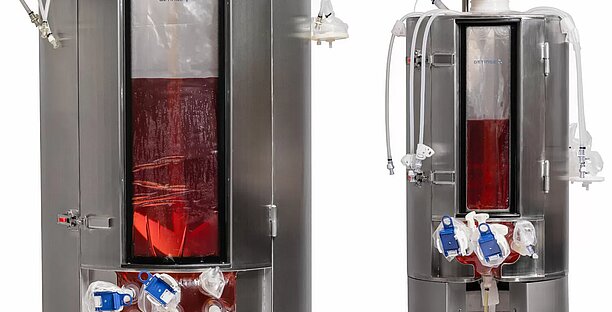
The SUPR bioreactor is available in the sizes 50L, 250L and 1000L.
AppliFlex ST single use bioreactors
Thanks to 3D printing technology, each AppliFlex ST bioreactor can be uniquely configured to your individual process which includes custom impeller designs and various port connections.
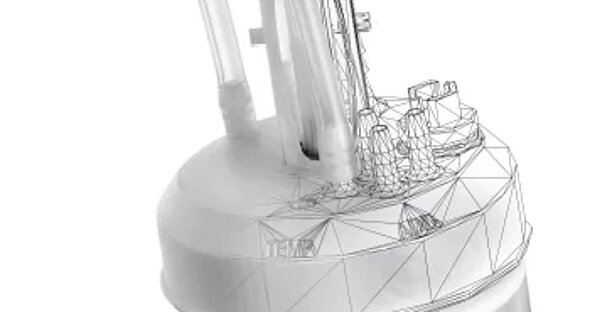
The AppliFlex ST bioreactors come in 500 mL, 3 liter and 15 liter volumes. They are produced according to the high-quality Applikon standard and are interchangeable with Applikon’s glass bioreactors of the same volume.
Mini bioreactors MiniBio
The MiniBio is a true scale down of the traditional lab-scale bioreactor. The reactor is available in 250 mL, 500 mL and 1000 mL volumes and customizable to meet the demands of any bioprocess. It saves time, requires minimal bench space and generates more data with fully scalable results.

Despite its small footprint, the MiniBio can meet any process requirements. Whether for Batch, FedBatch or perfusion processes.
Glass autoclavable bioreactors
The Applikon autoclavable bioreactor is a very popular bioreactor. It is available in 2, 3, 5, 7, 15 and 20-litre volumes. It is easy to adapt if your research changes. Thanks to the modularity and flexibility of the glass bioreactors, you can modify the system to fit any adaptations in process demands.
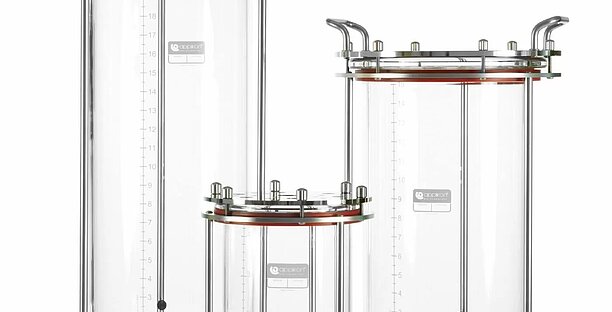
The glass bioreactors help support and optimise your research and process development. The systems are suitable for both cell culture and microbial culture applications.
Livit Flex bioprocess control system
The Livit Flex bioprocess controller is an intuitive and easily configurable bioprocess controller that fits any biotech upstream R&D application. Livit Flex can be configured as a single or dual control system for single-use or multi-use bioreactors to optimize bench space in the laboratory.
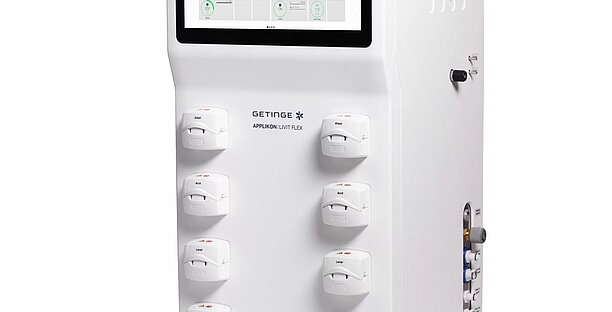
Livit Flex is ideal for use with single-use and reusable bioreactors up to 20L as well as our single-use pilot reactors.
my-Control
This colorful controller with the built-in web server is the ideal solution for small scale bioreactors starting at 50mL working volume. It uses minimal bench space and allows parallel bioprocessing for microbial as well as cell cultures.
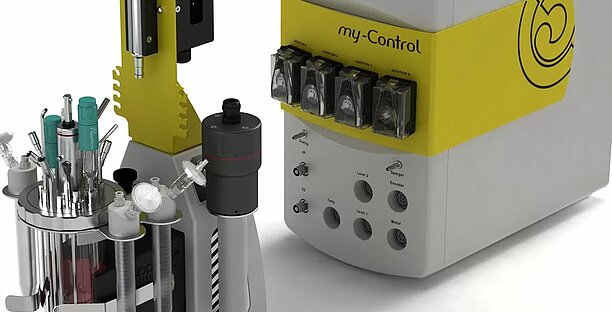
The myControl is the perfect solution for screening, process optimization or media development.
We are eager to receive your feedback
* Mandatory fields