Applications
Microbial bioreactor: harnessing microbial potential
The Applikon Mini bioreactor embodies the essence of microbial fermentation technology, facilitating the cultivation of microorganisms on a very small scale. It serves as a bacterial fermenter and yeast bioreactor, proving instrumental in the production of a wide array of bioproducts ranging from pharmaceuticals to biofuels. This bioreactor combines precision control with flexibility, allowing researchers and industrial biotechnologists to fine-tune environmental parameters such as temperature, pH, oxygen levels, and agitation to meet the specific needs of various microbial strains. The MiniBio allows researchers to generate very precise and valuable data on extremely small bench space, thus providing the basis for large-scale production.
The process of microbial fermentation in the Applikon mini bioreactor
Initialization and Sterilization
Before any operations commence, the Applikon Mini bioreactor is prepared and assembled, sensors are calibrated and the bioreactor is sterilized. Sterilizing the bioreactor in an autoclave ensures a sterile environment and guarantees that all system components are free of unwanted contaminants. The integrity and purity of your microbial culture provides the basis for successful fermentation outcomes.
Inoculation: Establishing the Basis for Uniform Fermentation
Inoculation starts with introducing a carefully prepared microbial seed culture. The Applikon Mini bioreactor's design ensures optimal mixing time to ensure an optimal inoculation into the culture medium. This lays the groundwork for uniform microbial growth and high yields. Precision is crucial for establishing an initial cell population that exploits the full capacity of the bioreactor for consistent fermentation.
Optimal Growth Conditions
The bioreactor accurately controls the environmental conditions necessary for microbial growth and metabolite production:
- Temperature: Customizable control systems tailor temperatures to the metabolic needs of different microbial strains, ensuring optimal enzymatic activity.
- pH: Continuous monitoring and automatic adjustment of pH levels are critical for maintaining enzymatic stability and overall microbial health.
- Dissolved Oxygen: Oxygen transfer rates are finely tuned according to the aerobic or anaerobic needs of the microbes. Ensuring sufficient oxygen availability for aerobic cultures while preventing oxidative stress.
- Agitation: Two rushton impellers ensure a homogeneous mix of nutrients and cells, facilitating effective gas exchange and preventing cell sedimentation, enhancing overall metabolic efficiency.
Nutrient Feeding Strategy
The Applikon Mini bioreactor supports versatile nutrient feeding strategies, including batch, fed-batch, and continuous modes, allowing precise control over nutrient supply. These strategies maximize product yields and maintain prolonged microbial productivity while minimizing the formation of undesirable by-products and metabolites. Automated feeding systems adjust nutrient delivery based on real-time measurements of biomass concentration and metabolic activity, optimizing growth conditions and boosting fermentation efficiency.
Monitoring and Control
Equipped with cutting-edge sensors, the Applikon Mini bioreactor offers real-time monitoring of critical parameters such as pH, oxygen levels, and temperature. Continuous surveillance enables timely adjustments, ensuring the culture develops under optimal conditions until the desired cell density or product concentration is achieved.
Advantages of the Applikon mini bioreactor for microbial fermentation
The Applikon Mini bioreactor, offers several advantages for microbial fermentation:
- Scalability: Its design supports the seamless scale-up of microbial processes from research to production scale. Applikon's product portfolio scales from mini bioreactors with 50mL working volume to large-scale stainless steel bioreactors with 5000L volume.
- Flexibility: Accommodates a wide range of microbial types and fermentation strategies, including aerobic or anaerobic organism or culturing yeast for organic processes.
- Control and precision: Advanced control systems enable precise manipulation of environmental conditions, enhancing microbial productivity and product consistency.
- Efficiency: Optimized for high-density cultures and high-yield product recovery, making it a cost-effective solution for microbial fermentation.
Benefits of Using the Applikon Bioreactor
The Applikon Mini bioreactor represents a highlight of bioreactor engineering, perfectly suited for the demands of microbial fermentation. Its advanced features ensure that microbial fermenters can achieve high yields of biomass or bioproducts, making it an indispensable tool in the biotechnological industry. Whether for bacterial or yeast cultures, the Applikon Mini bioreactor provides a reliable and efficient platform for bioreactor fermentation, advancing the capabilities of researchers and producers in the vibrant field of microbial biotechnology
Feautured Products
Stainless steel bioreactors
Stainless steel bioreactors play a key role in the development and production biotech products. From bench to pilot to full production – the Applikon bioreactors simplify your scale-up through consistent design and scalable control solutions.
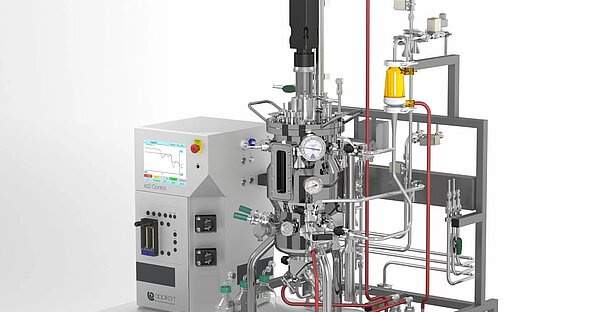
Our portfolio offers both standard systems for fermentation and cell cultures as well as customized systems.
Glass autoclavable bioreactors
The Applikon autoclavable bioreactor is a very popular bioreactor. It is available in 2, 3, 5, 7, 15 and 20-litre volumes. It is easy to adapt if your research changes. Thanks to the modularity and flexibility of the glass bioreactors, you can modify the system to fit any adaptations in process demands.
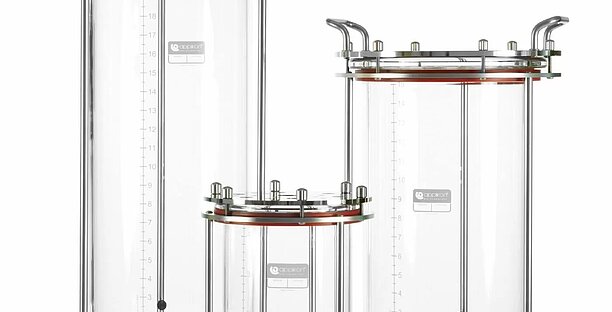
The glass bioreactors help support and optimise your research and process development. The systems are suitable for both cell culture and microbial culture applications.
Mini bioreactors MiniBio
The MiniBio is a true scale down of the traditional lab-scale bioreactor. The reactor is available in 250 mL, 500 mL and 1000 mL volumes and customizable to meet the demands of any bioprocess. It saves time, requires minimal bench space and generates more data with fully scalable results.

Despite its small footprint, the MiniBio can meet any process requirements. Whether for Batch, FedBatch or perfusion processes.
Livit Flex bioprocess control system
The Livit Flex bioprocess controller is an intuitive and easily configurable bioprocess controller that fits any biotech upstream R&D application. Livit Flex can be configured as a single or dual control system for single-use or multi-use bioreactors to optimize bench space in the laboratory.
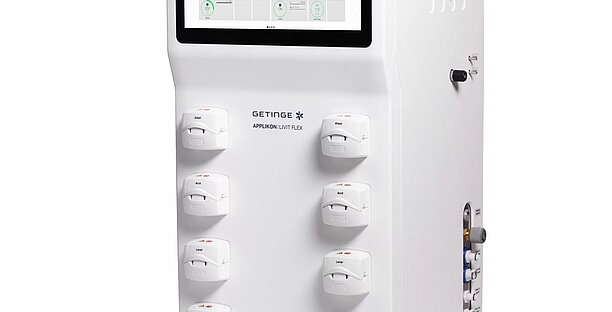
Livit Flex is ideal for use with single-use and reusable bioreactors up to 20L as well as our single-use pilot reactors.
AppliSens Sensors
Our portfolio includes a range of sensors to get the optimum data from your process. They provide important information that impacts the viability and productivity of the cells and influences the quality of the end products.
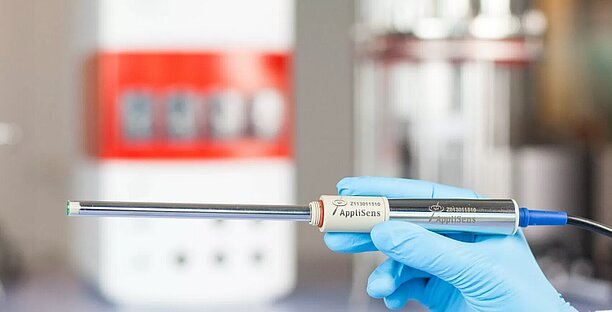
The intelligent and optical sensors can be integrated seamlessly into your system and provide you with real-time data for precise control of your bioprocess
We are eager to receive your feedback
* Mandatory fields