Applications
The Viral Vector Manufacturing Process Explained
The production of viral vectors involves several critical stages, each requiring careful scientific monitoring:
Design and recombinant vector construction
Initially, a therapeutic gene is inserted into a plasmid vector containing the necessary viral genetic elements. This recombinant vector is designed to utilize the natural viral lifecycle while ensuring the delivered gene's expression in the target cell without causing disease.
Transfection and viral packaging
Subsequent steps involve the transfection of a producer cell line with the recombinant vector. These cells are engineered to express viral structural proteins, packaging the therapeutic gene into viral particles. This stage is crucial for the initial generation of viral vectors and requires optimal transfection conditions, which are precisely maintained in the AppliFlex ST single-use bioreactor through controlled parameters.
Amplification and harvest
The transfected producer cells are then cultured under ideal conditions that promote viral vector replication. The AppliFlex ST single-use bioreactor facilitates this process by providing an environment with strictly regulated temperature, pH, dissolved oxygen levels, and other parameters, which are essential for maximizing viral titers while maintaining cell viability.
Purification and concentration
Following amplification, the viral vectors are isolated from the cell culture medium through a series of purification steps, including ultracentrifugation, chromatography, and filtration. These processes aim to eliminate contaminants and concentrate the viral vectors, ensuring their purity and potency for therapeutic use.
Quality assessment
The final product undergoes a comprehensive battery of tests to assess its safety, purity, concentration, and biological activity. These include assays for viral titer, vector genome integrity, and potential contaminants, ensuring that the viral vectors meet stringent regulatory standards for gene therapy applications.
Why the AppliFlex ST Single-Use Bioreactor Is Essential for Viral Vector Research and Development
The AppliFlex ST single-use bioreactor is pivotal in the viral vector manufacturing process, offering several advantages:
- Precise environmental control: It enables the fine-tuning of culture conditions, such as temperature, pH, and dissolved oxygen levels, which are critical for optimizing transfection efficiency and viral production.
- Scalability: The bioreactor's scalable reactor design allows for scale-up, facilitating the transition from small-scale experimental batches to larger volumes required for clinical applications.
- Efficiency: Advanced monitoring and control features increase viral vector production's overall efficiency and yield, streamlining the process from initial development to commercial-scale manufacturing.
- Versatility: The AppliFlex ST single-use bioreactor can support a wide range of viral platforms and cell lines and is adaptable to various gene therapy viral vector manufacturing requirements.
- Pre-sterilized single-use system: The closed system offers sterile conditions and guarantees process safety and reduces the risk of contamination.
Benefits of Using the Applikon Bioreactor
The scientific complexity of viral vector manufacturing underscores the necessity for precise control and optimization of the research and development process. The AppliFlex ST single-use bioreactor stands at the forefront of biotechnological advancements, providing an indispensable tool for researchers and manufacturers engaged in the development of viral vectors. Its capabilities ensure that the complex requirements of viral vector research are met with unique precision, facilitating the advancement of genetic engineering. Further information on the Applikon Mini bioreactor and its applications in viral vector research and development can be found at AppliFlex ST single use bioreactors - Resea Biotec GmbH.
Feautured Products
AppliFlex ST single use bioreactors
Thanks to 3D printing technology, each AppliFlex ST bioreactor can be uniquely configured to your individual process which includes custom impeller designs and various port connections.
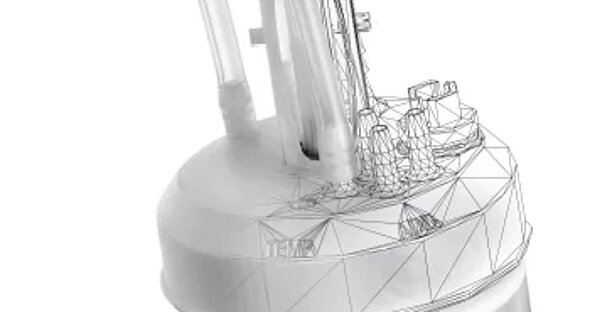
The AppliFlex ST bioreactors come in 500 mL, 3 liter and 15 liter volumes. They are produced according to the high-quality Applikon standard and are interchangeable with Applikon’s glass bioreactors of the same volume.
V-Control
Developed in partnership with Emerson, V-Control is a process control platform designed as a 'one common-platform' solution for bioreactors from research to production.
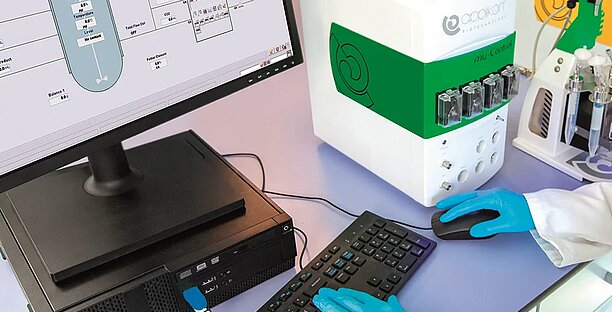
V-Control offers a scalable software solution that overcomes the hurdles of scaling up.
SUPR single-use bioreactor
The SUPR single-use production bioreactor impresses with its simple, scalable and customer-friendly design. The cell culture reactor enables a seamless process transfer from R&D to production.
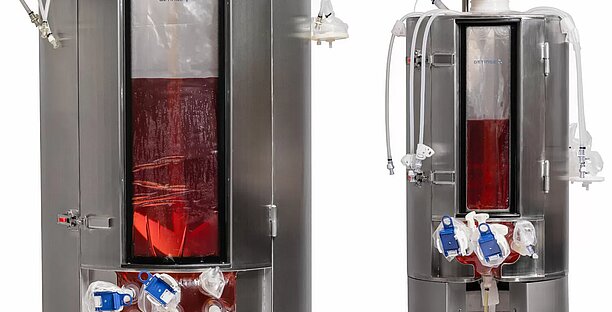
The SUPR bioreactor is available in the sizes 50L, 250L and 1000L.
AppliFlex ST GMP single-use bioreactor
The AppliFlex ST GMP is a configurable single-use bioreactor that meets all cGMP requirements for clinical production. The system simplifies Scale-Up, Scale-Down and Scale-Out. The fully closed system is customizable and reduces any risk of cross contamination.
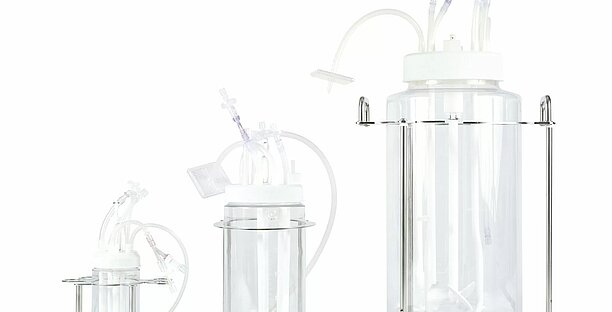
The AppliFlex GMP is available in 500 mL and 3 L versions for both cell cultures and microbes.
Livit Flex bioprocess control system
The Livit Flex bioprocess controller is an intuitive and easily configurable bioprocess controller that fits any biotech upstream R&D application. Livit Flex can be configured as a single or dual control system for single-use or multi-use bioreactors to optimize bench space in the laboratory.
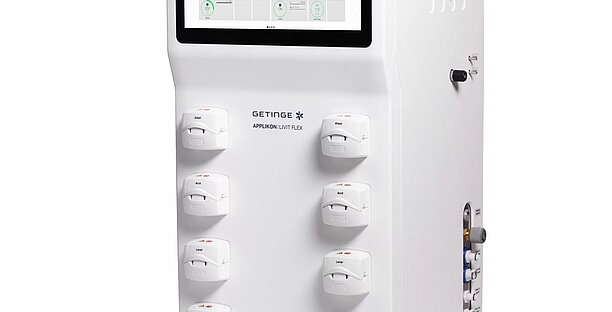
Livit Flex is ideal for use with single-use and reusable bioreactors up to 20L as well as our single-use pilot reactors.
We are eager to receive your feedback
* Mandatory fields